Corrugated Packaging Basics
Corrugated boxes are ubiquitous across packaging applications, providing a sturdy yet cost-effective means of transporting and storing goods. At Imperial Paper, we have 57 years of experience in designing and manufacturing premium corrugated packaging, retail bags, point-of-purchase displays, and shipping supplies through fair and ethical business practices.
In this guide, we’ll cover the basics of corrugated materials to help you determine which packaging solution is right for your needs.
What Are the main corrugated materials?
Corrugated materials are available in a range of thicknesses and strengths. Most corrugated materials consist of two or more facing layers with corrugated flutes sandwiched between them. However, a single-face sheet is a simple corrugated material that combines one sheet of liner board facing with one layer of flute and is primarily used for protective wrapping or packing.
Far more common are single, double, and triple-wall corrugated materials, which together form the vast majority of corrugated boxes used today.
Single Wall Corrugated Material.
Single wall corrugated material consists of two layers of linerboard facing adhered to either face of a flute layer.
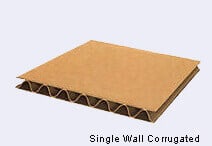
Double Wall Corrugated Material.
Double wall corrugated material is even sturdier than a single wall as it adds an extra layer of flute and an extra linerboard facing. Double-wall corrugated materials are a good choice for stacking heavy materials.
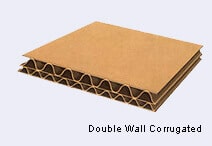
Triple Wall Corrugated Material.
Triple wall corrugated material is a heavy-duty option that comprises three layers of flute layered between four sheets of facing. Triple-wall corrugated material is strong, crush-resistant, and ideal for both shipping and stacked storage.
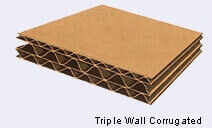
All of these constructions are available with a variety of external liners, depending on printing needs. The most common exterior liner grades include:
- Kraft. Naturally brown, this is the most commonly used and least expensive liner.
- #3 White. This liner is mottled white, with underlying kraft showing through. It provides a cleaner look and better printability than kraft.
- #1 White. This liner is bleached bright white and offers very good printability, but it easily soils during transit.
- Premium Grades. Premium grade liner surfaces have a bright white clay coating, minimizing porosity to allow printing inks to sit up on the surface. It gives excellent printability as colors are more vibrant, and lower absorbency improves registration. However, because of the high hold-out, ink rub can be a problem.
- Litho-printed Labels. These are used for labels laminated onto corrugated boxes.
What are corrugated flutes?
A corrugated flute is a folded material that sits in between the liners to stabilize and cushion the structure. Corrugated flutes differ in size and profile based on the number of folds, or flutes, per foot, giving rise to several standard sizes:
- A Flute. This flute profile is the thickest size, meaning it has the fewest folds per foot. Its excellent cushioning and stacking properties make it ideal for various customer uses.
- B Flute. B flute has excellent crush resistance and offers a flat, stiff surface suitable for high-quality printing and die cutting.
- C Flute. C flute is the most widely used flute profile as it offers excellent cushioning, stability, and print quality.
- E Flute. E flutes are thin and stiff, making them ideal for uses where space constraints are a primary concern.
- F Flute. F flute is the thinnest common flute size and was originally developed to minimize fiber count.
Generally, larger flute profiles give greater cushioning and vertical strength, while smaller ones offer greater structural integrity and better print quality. Different flute profiles can be combined in one piece of combined board. For instance, our double wall board uses a B-C flute combination.
What corrugated box styles fit what applications?
The box style you choose depends on your application. A comprehensive list of box types, uses, and abbreviations is available in our knowledge center, but the following overview should help familiarize you with the common types and terms.
Slotted Boxes
Slotted boxes are made from single pieces of scored and slotted corrugated blanks for easy folding. RSC (regular slotted containers) are the most common, featuring equally sized flaps that meet in the middle when folded together. However, FOL (full-overlap slotted) and SFF (center special full-overlap slotted) boxes offer the best cushioning and stacking potential. Slotted boxes are a reliable choice for most standard packaging and shipping applications. Other varieties include HSC, OSC, CSSC, CSO, and more.
Telescoping Boxes
Telescoping boxes have a separate lid and bottom and come in a variety of shapes and sizes. Combining different lid and body shapes allows telescoping boxes to fit many irregularly shaped or heavy products, such as refrigerators, water heaters, and more. Most telescoping boxes are square or octagonal, with octagonal being the better choice for round objects.
Folders
Folders are usually a single sheet of corrugated board with scores for easy folding. One-piece folders (OPF) are the simplest and come with or without Air Cell flaps, while five-panel folders (FPF) offer additional cushioning and stacking potential. There are also enforced and stackable display trays, which are often used as inner containers for parts.
Rigid Boxes
Also known as bliss boxes, rigid boxes are three-piece shipping containers combining two identical end panels with a body panel. These pieces are bonded using cold adhesive, hot melt, or a combination of the two. These are a great choice for large or heavy shipments and offer cost-effectiveness without sacrificing box performance.
Self-Erecting Boxes
Self-erecting boxes are distinguished by an attached, foldable lid, which may resemble either an RSC or a telescope-style top once assembled.
Interior Forms
Interior forms such as pads, tubes, and partitions sit inside a larger box to separate or pad contents. Interior forms may be used to hold products in place during shipping or to separate products within marketing displays.
Bulk Bins
Bulk bins are large corrugated fiber boxes used to consolidate a large number of smaller packages. Bulk bins promote efficiency in high-volume handling applications.
Does ink color matter?
Many clients choose corrugated materials for custom packaging, which often involves complex printed graphics. The choice of ink can be critical to the success of these projects. From a marketing standpoint, color is one of the most striking features of your brand’s visual identity, so it’s important to consider peoples’ emotional reactions to specific colors and identify colors that align with your overall image.
Certain colors offer various benefits for printing. For example, using standard 60 Glass Container Manufacturers Institute (GCMI) colors for low-volume production runs offers consistency, lower costs, and ease of duplication.
How to Print on Corrugated Cardboard
There are three primary methods of printing on corrugated boxes, and the best method depends on your desired print quality, graphic complexity, and similar factors.
- Flexographic Relief Printing. This method is best for edge-to-edge or text-heavy prints, offering good image fidelity at an affordable cost.
- Lithographic Offset Printing. This method is more expensive, but it allows for higher-resolution graphics.
- Digital Printing. Digital printing is a lower-cost option that uses cyan, magenta, yellow, and black (CMYK) for quick and accurate printing; however, it could lead to vibrancy issues and color imperfections.
WHAT BOX DIMENSIONS ARE BEST?
When purchasing corrugated boxes, there are two essential sets of measurements to keep in mind. The internal box dimensions must be large enough to fit the product and all necessary packaging, while the outer dimensions dictate how many boxes will fit in a given vehicle, pallet, or storage unit. Always report the inner dimension unless you have a specific reason to also specify the outer dimension, in which case you should label the outer dimensions with “OD.”
THE BEST BOX CLOSURE METHODS
Corrugated boxes can be sealed using a variety of methods, depending on the contents and potential handling concerns.
- Tape. Perhaps the most common sealing option, the tape is cost-effective and adds extra protection against moisture. PVC tapes tend to be the most durable, though polypropylene tape may be more cost-effective.
- Staples. Staples are cost-effective and can be applied rapidly for efficient packaging at high volumes. Staples also better secure the box against tampering when compared to tape.
- Straps. Used primarily for securing pallets, straps can hold boxes shut on their own or in combination with other closure methods.
- Glue. Hot melt glue is often used to seal the bottoms of boxes, offering a stronghold that can withstand rough handling.
HOW TO STORE & HANDLE BOXES
Although corrugated boxes aren’t necessarily fragile, proper handling can prolong their life and protect their contents. Empty boxes should be stored flat on a clean surface. Ensure that the storage area is dry and kept at a consistent temperature to avoid damaging the paper. Avoid storing the boxes upright or stacking other materials on top of the box, as uneven weight distribution may crush the flutes.
Full boxes on pallets should be secured with stretch film and straps to protect against moisture or falls. Ensure that boxes are stacked evenly and away from overhang so that the weight distribution remains even.
CUSTOM CORRUGATED BOXES FROM IMPERIAL PAPER
Imperial Paper offers a wide range of premium corrugated boxes, including customizable options for subscription boxes and more. We use the latest technology to create packaging solutions to suit your exact needs. To learn more about our products and services, contact us or request a quote today.